Anfertigung der Leisten
Geschrieben am 08.05.2015 in Holzkanubau — Holzkanu, Leistenkanu (Geändert am 05.07.2017)
Teil 3 von 7 in der Serie Bau eines Großcanadiers
Inzwischen war es Mitte Februar geworden, und ich hatte immer noch Zeit. Bei einem Holzhändler holte ich mir rohe Kiefernbretter 25x150 mm, die ich abrichtete und anschließend durch meinen Dickenhobel fuhr, bis sie alle eine Stärke von 21 mm erhalten hatten. Ich hatte trockene, so gut wie astfreie Tischlerware.
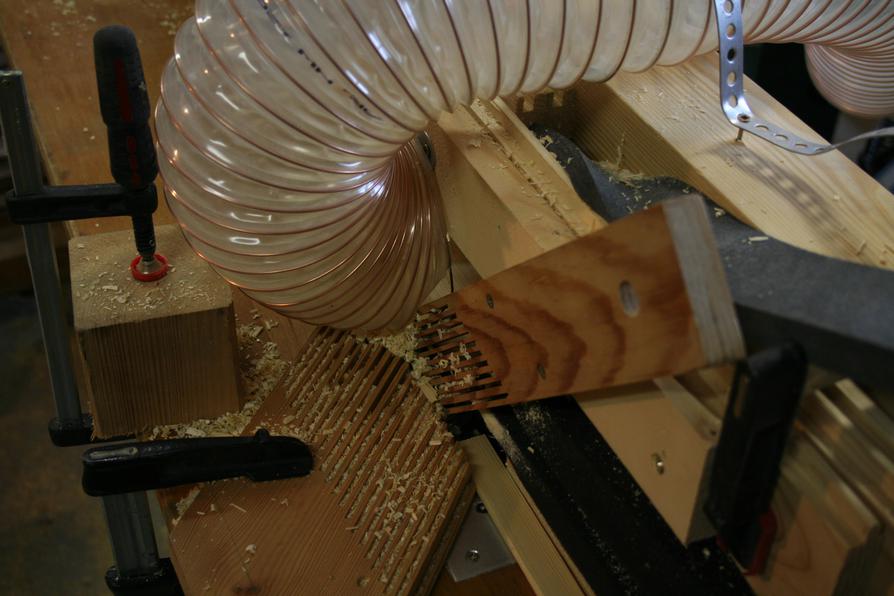
Holzkanubau: die Leisten Konterprofil-Fräsen: Die Leisten für die Beplankung bekommen ein Konterprofil auf jeder Seite: eins mit konvexem, die andere mit konkavem Profil. Dafür habe ich einen speziellen Satz Schaftfräser anfertigen lassen, der genaue Rundungen entstehen läßt. Die Fräseinrichtung besteht aus einer 1200 Watt Aldi-Oberfräse, für die ich eine rechteckige 3-mm-Aluplatte als Fußplatte gefertigt habe, die die serienmäßige Fußplatte ersetzt. Die neue Platte habe ich bündig in eine Dreischicht-Platte 26mm eingelassen, Als Anschlag habe ich mir ein vorhandenes Kantholz 100x200mm auf den provisorischen Frästisch gespannt, das eine 13mm starke Sperrholzleiste mit Aussparung für den Fräskopf festklemmt. Die Druckkämme ermöglichen entspanntes Arbeiten, man schiebt einfach die 500m Leisten nacheinander durch. Eine 2. Person hätte ich mir gewünscht, zum Wegordnen der fertigen Leisten.
Von diesen nunmehr 4-seitig gehobelten Brettern sägte ich ca. 8 mm dünne Leisten herunter. Diese fuhr ich noch beidseitig durch den Dickenhobel, bis sie eine Stärke von 6,3 mm hatten. Diese Nennstärke ist durch meinen Fräsersatz vorgegeben, den ich mir in England gekauft habe. Die Art der Fertigung meiner Plankenleisten ergab fast auf jeder Leiste stehende Jahresringe: die Bretter zeigten Fladern, die davon herunter geschnittenen Leisten haben dann stehende Jahre.
Zum Anfräsen des konvex-konkav-Profils nutzte ich meine selbst gebaute Maschine, deren Kern aus einer schweren 12-mm Oberfräse bestand. Ich montierte allerlei Einrichtungen zum Absaugen sowie Andrück-Kämme. Dann fräste ich die ca 500 Meter Leisten zuerst von der konkaven, dann von der konvexen Seite.
Es gab dabei einige Schwierigkeiten: erstens musste ich die 500 Meter Leisten "verwalten". Um das zu bewerkstelligen, baute ich mir ein Konsolenregal provisorisch in etwas erhöhter Position, so dass ich eine schnell zu nutzende Ablagemöglichkeit bekam.
Die nächste Schwierigkeit war, dass die hauchdünnen Kanten der Leisten nach der konkaven Kehlung keine gute Anlagemöglichkeit am Anschlag boten. Es hat trotzdem alles funktioniert, aber für einen Tischler ist so etwas grausig, und es verlangsamt auch die Durchlaufgeschwindigkeit. Es bremst, und es fühlt sich nicht schön an. Sollte ich wieder einmal solch ein Profil fräsen wollen, werde ich mir ein konvexes Gegenstück auf meinen Fräsanschlag leimen.
Die Druck-Kämme haben bestens funktioniert, ebenso wie die Absaugeinrichtung. Ich konnte meine Leisten einfach alle hintereinander am Fräskopf vorbei schieben, also auch die fertige Leiste mit der neuen ganz durchschieben.